Learn more about Calibre 9S
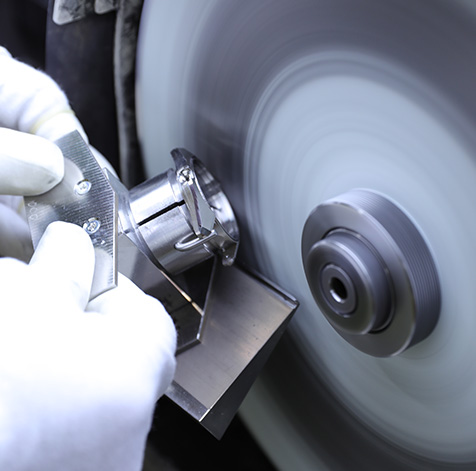
Zaratsu polishing. An art perfected over decades.
In Zaratsu polishing, the craftsman presses the surface to be polished against the front of the rotating disc. The disc of course rotates at an even speed but the polisher uses the fact that the disc moves more quickly at its edge than in the center to achieve the desired distortion-free result; by moving the surface of the case towards or away from the center of the disc, very subtle and exact surfaces and edges can be made. Even the slightest differences in the pressure applied or in the angle at which the case is held cause the case to change in appearance. It takes the highly accomplished skills of veteran artisans to be able to re-create the exact same effect on each case. The polishing machines used for this Zaratsu process were brought in from external suppliers half a century ago but none of them remain today, having been replaced by Seiko’s own, proprietary machines. These new machines have higher specifications and enhanced capabilities, including the capacity to allow the operator to set the number of revolutions of the disc to the level that best suits each task. The craftsmen also use polishing compounds which were developed by the Grand Seiko team after much trial and error to work well on both stainless steel and high-intensity titanium surfaces.
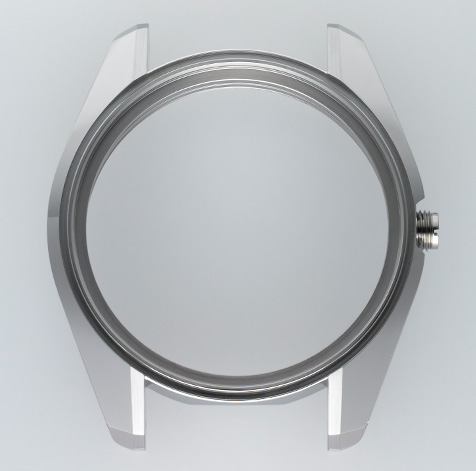
The long journey from raw metal to finished watch case.
Every case destined to be home to a Calibre 9S movement is first formed by a 300-tonne cold forging press. The details are then gradually shaped through the use of several dies while repeatedly subjecting the case to heat treatment at temperatures over 1,000 degrees Celsius. Then comes a further refinement process using a CNC (computer numerical control) machine. It should perhaps be called Metal Sculpting by Machine; each stage of precision machining peels off about 0.1 millimeter of the surface of the forged case. The final process is polishing. While each design has its own profile, an average of fifty separate polishing stages is required. The second to last step of this process is the Zaratsu polishing, which prepares the surface to be buffed to a mirror-like finish.
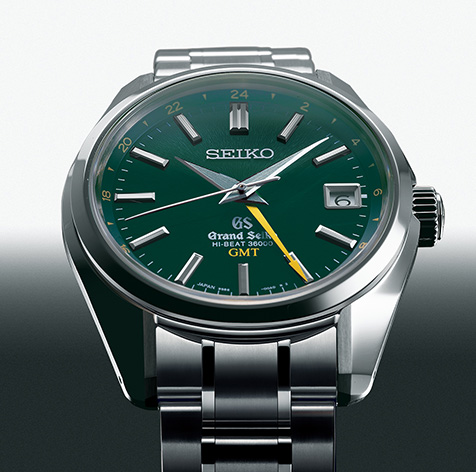
The Petite Aiguille award
October 2014. At the Grand Prix d’Horlogerie de Genève, Grand Seiko’s Mechanical Hi-Beat 36000 GMT Limited Edition was awarded the Petite Aiguille prize. This timepiece fitted with the 9S86 calibre was designed by Nobuhiro Kosugi who, earlier that same year, had been awarded the title of Contemporary Master Craftsman by the government of Japan. The movement was assembled in the Shizukuishi Watch Studio in Iwate Prefecture while the case was manufactured in a factory in Fukushima. Particularly after the devastation that the region had suffered after the Tohoku earthquake in 2011, this award was greatly appreciated by the craftsmen and women at both facilities as a tribute to their watchmaking prowess and determination to overcome all obstacles.