Spirit and Skill In the Shadow of Mt. Iwate
In the winter of 2022, amidst snowfall heavier than in normal years, the peak of Mt. Iwate was itself covered in a thick layer of white. Situated on a site with a commanding view of this scenery is the Grand Seiko Studio Shizukuishi. This new production base was opened by Morioka Seiko Instruments in 2020, helping to mark the milestone 60th anniversary of Grand Seiko. Embodying the brand’s philosophy, “The Nature of Time,” the assembly and adjustment of Grand Seiko mechanical timepieces are carried out in a wooden cleanroom the likes of which are rarely found anywhere else in the world.
Surrounded by this lush natural environment, conversation among the craftsmen inevitably starts with the morning view of Mt. Iwate, just as if they were talking about the weather that day.
In the words of President Yoshiaki Hayashi:
“Mt. Iwate has a symbolic presence, and being close to it seems to stimulate conversation. The studio’s lighting is exquisite, with the surrounding natural vista inevitably slipping into one’s field of vision when glancing away from work. From the perspective of spiritual refreshment as well, a truly outstanding environment has been realized here.”
As this facility moves into its second spring following the move to full-fledged operations, the sense of harmony with nature inevitably comes to mind.
“Snowfall was especially deep in 2022, further driving home the reality that natural conditions are keenly impacted by the ever-changing weather. For human beings to survive and prosper, it is important to both live in harmony with and to fear Mother Nature. I feel that such sensations are likewise vital in the dimensions of everyday life and watchmaking.”
Facing nature, a force that rarely moves according to plan, makes people humble while developing tenacity and honesty. Adds President Hayashi: “That is also a trait shared by the people of Iwate Prefecture, raised in the lap of this rich natural setting, as well as an attribute embedded in Grand Seiko.”
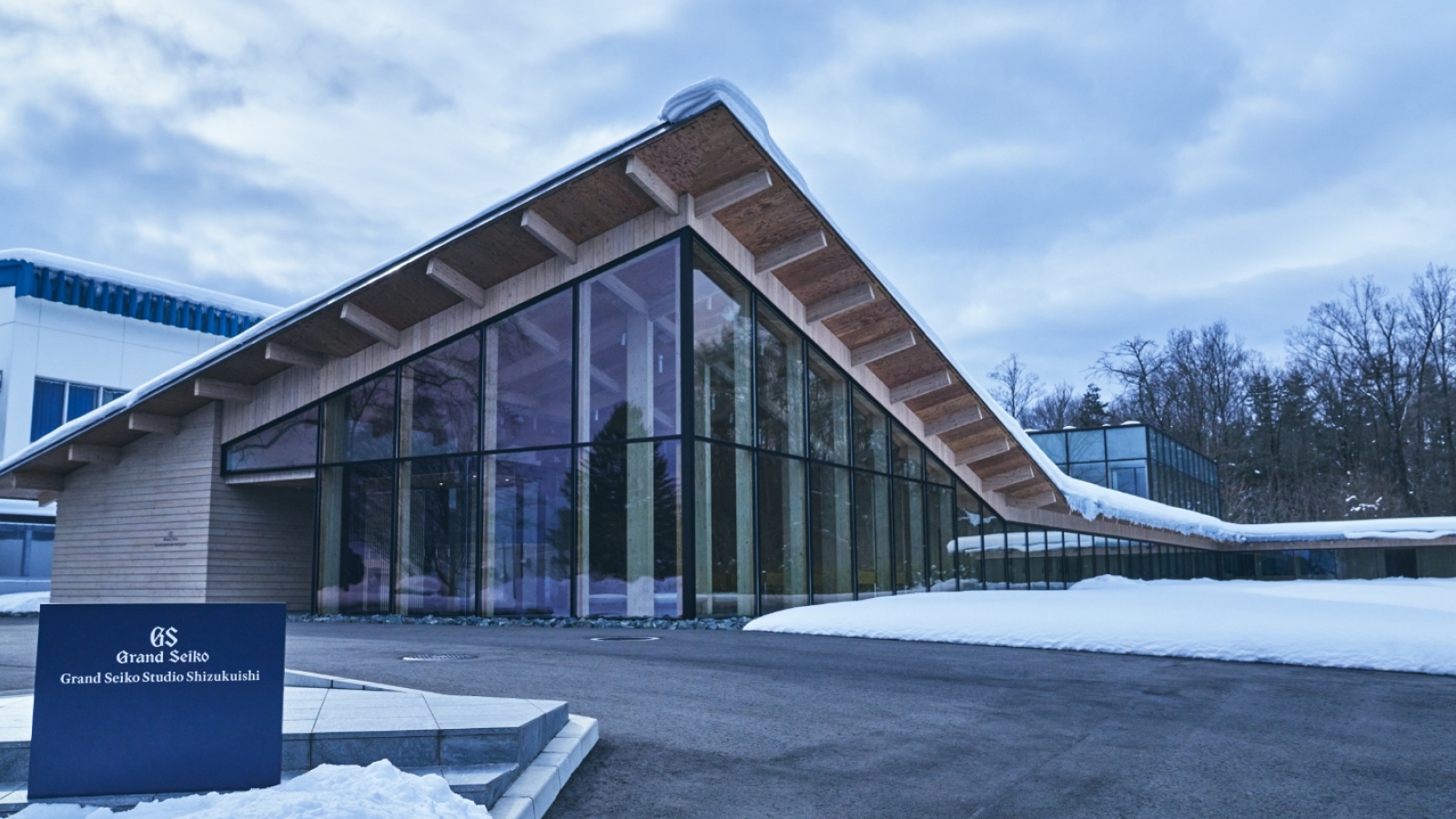
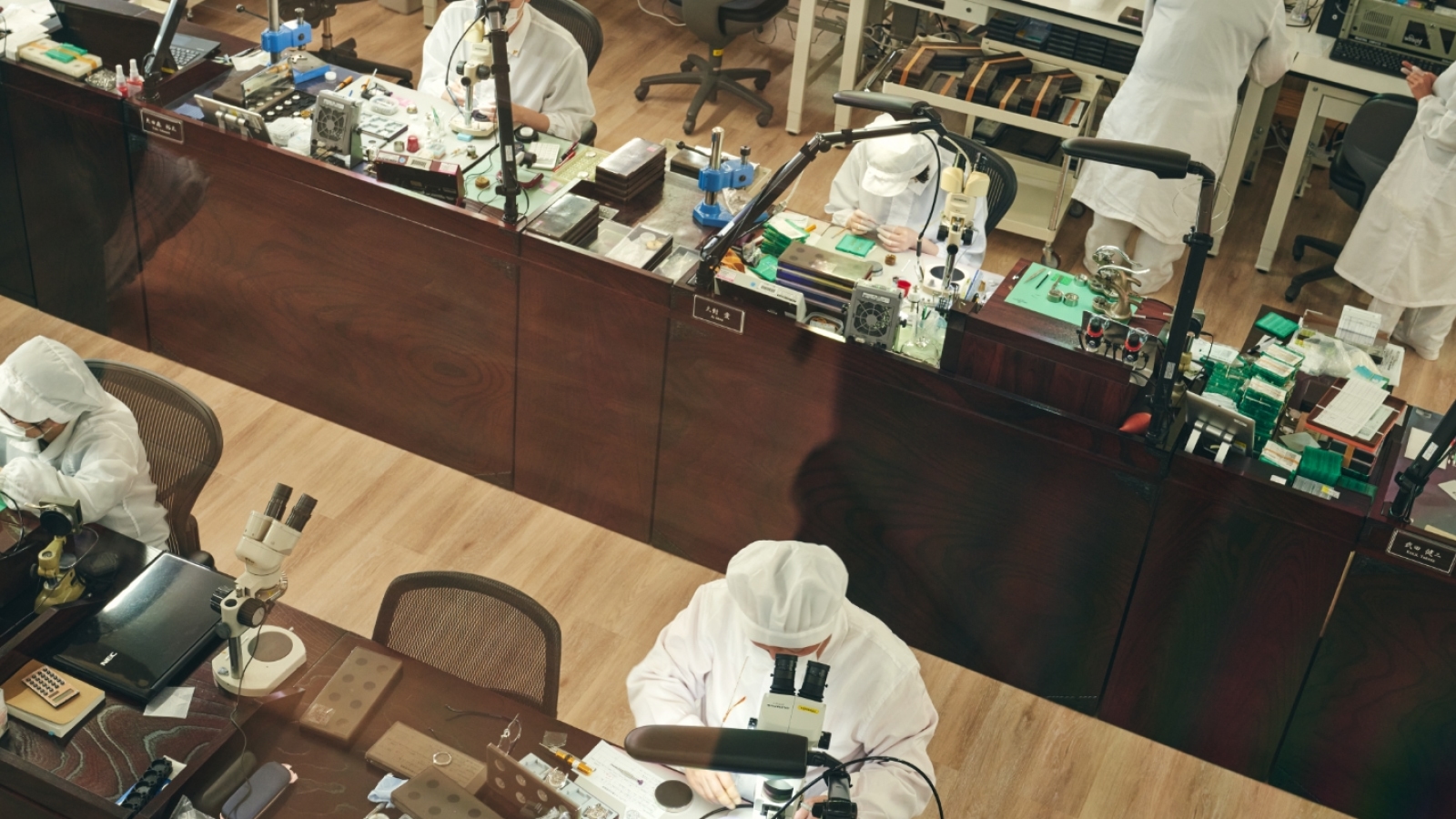
The cleanroom work desks are veritable symbols of the studio’s quest for immaculate symbiosis and harmony with nature. Treated with penetrating lacquer to coax out the exquisite wood grain, their appearance is like that of antique furniture, while radiating unique hues within a space devoted to cutting-edge inspection and measuring instruments. These items of rare beauty reflect the techniques of Iwayado Tansu.
These origins may be traced back to the Kowa Era of Japanese history (around 1100). The business is said to have emerged in the Tenmei Era (decade of the 1780s). This is when Muramasa Iwaki, feudal lord of Iwayado (the current-day Esashi district of Oshu City in Iwate Prefecture), issued a decree to promote local industrial development. From ancient times, this was a region noted for outstanding lacquering techniques using the wood from rich forests of Japanese zelkova, paulownia, and other trees flourishing there. Along with this, metal fittings used to produce keys and other items were mobilized in the delicate engraving and casting of dragons, tigers, birds, flowers, and other ornamental decorations. Through the use of extensive craftsmanship spanning woodwork, lacquerwork, ironwork, and other genres, the achievements of this district eventually rose to nationwide fame.
However, the distinctive characteristics of the area were not limited to these exploits. In the quest to carry on these traditions following World War II, local producers banded together to form industrial cooperatives. The forces of stable production and friendly competition served to steadily raise quality, while the introduction of an original craftsman certification system was instrumental in promoting studies of techniques and the cultivation of individual producers. Against this backdrop, the emerging products were not limited to traditional tansu (chests of drawers), expanding to cabinets, television stands, and various other items matched to modern lifestyle environments, the popularity of which has spread overseas as well. The timeless appeal of these creations earned a stellar following as so-called “modern antiques.” Penetrating throughout all aspects of these pieces was the passing on of traditions nurtured by the natural features and history of Iwate, along with ingenuity connecting to the next generation. These characteristics may also be seen in the spirit and ingenuity of Grand Seiko.
Craftsmen Mesmerized by the Returning Desk
The encounter with Iwayado Tansu dates back to 2004, when Morioka Seiko Instruments established the Shizukuishi Watch Studio. The furniture is truly in keeping with Grand Seiko's specialized studio, which carries the local place name, so the craftsmen were instinctively drawn to Iwayado Tansu because it shares Grand Seiko’s values.
This coupled with the idea to transform its wares into specialized cabinets. Rising to meet this request was Nakasen Furniture Store.
Nakasen Furniture President Hiroaki Nakamura reflects on those days: “While the request called for creating an L-shaped standalone desk designed for work ease, this was our first encounter with angled specifications. The assembly work demanded ingenuity, while the layered lacquer coating was also a difficult challenge.”
These meticulously crafted work desks instilled warmth in the studio, where watchmakers went on to create numerous Grand Seiko pieces. In time, this workshop was transferred to the current new building.
Continues President Hayashi: “With the facilities set to become state-of-the-art, the opinion was voiced that this opportunity should be seized for a renewal of the desk maker as well. As it turned out, however, the on-site craftsmen favored continuing to use Iwayado Tansu. They cited roots lying in the area as a traditional studio, along with their desire to carry on the traditional craftsmanship for which Iwate Prefecture is renowned. I believe this can be traced to the familiarity of daily use and the resulting keen attachment nurtured over the years.”
In the quest for greater work efficiency, however, the specifications were shifted from the standalone type used to date to a straight, horizontal, flat surface. To achieve this transition, it was necessary to disassemble and essentially restructure the desks. With this work demanding considerable time and attention, even Nakasen Furniture Store was able to turn out only one or two pieces monthly.
“Despite that,” adds President Hayashi, “We were determined to succeed.” This work was advanced concurrently with the studio construction, as a full year was devoted to recreating the desk.”
Nevertheless, Nakasen Furniture Store craftsmen were deeply impressed when they set eyes on the returning desk. They reported that the fading hue of rich layers of lacquer applied in their daily work had been transformed into a lustrous state in which they sensed the spirit of accomplished watchmakers. With lovely lacquer once again applied on the surface, there was a palpable perception of the shared and unchanging passion of the creators. This fervent sentiment has also been channeled into Grand Seiko.

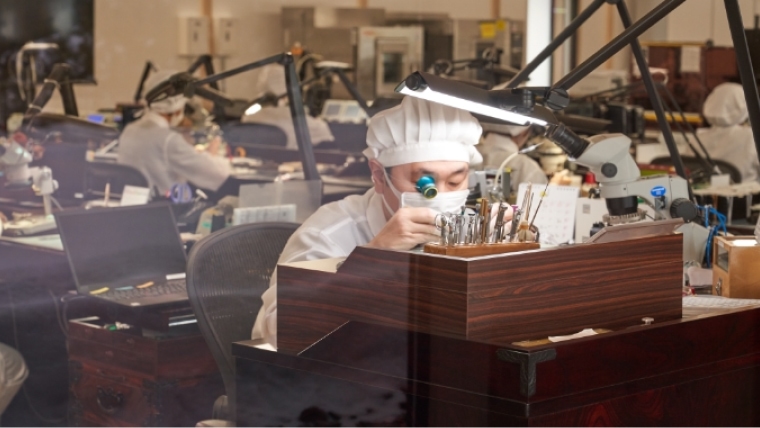
Upon the move to Grand Seiko Studio Shizukuishi, work desks were changed from standalone to straight, horizontal, flat-surface types.
From artisan to artisan. Steadily passing on craftsmanship.
Regardless of advanced equipment, an absence of individuals with skills matched to this hardware will fail to produce the desired results. Taking this reality to heart, Morioka Seiko Instruments has committed keen efforts to cultivating human resources and passing on skills. This includes the establishment of the previously mentioned Shizukuishi Watch Studio and the simultaneous introduction of the “Meister System.” Certified once every two years, the system not only strives to achieve high technology but also spans three separate ranks. Those holding credentials at each level designate successors to pass on their expertise and are required to devote their energy to the training of such apprentices over the long term.
While craftsmanship naturally demands accrued experience, the key to continuity lies in visualization and clarification of such qualities. Such endeavors spawned new fruits last year. The company’s Hideto Yamazaki was selected as an “Outstandingly Skilled Worker (Contemporary Master Craftsman)” in 2021. This “Master Craftsman” designation is a system under which Japan’s Ministry of Health, Labour and Welfare designates outstanding artisans once each year and is considered a recognition of those at the forefront of their fields.
Recognized as possessing particularly high value in the 2022 awards was the field concerned with parts production known as mold finishing. According to President Hayashi: “In the quest to raise the precision of watches as industrial products, it is critical to also achieve precision in the parts themselves. Regardless of how elevated human adjustment technology may become, there will inevitably be limits. In contrast, raising the precision of the parts themselves is the key to streamlining the adjustment work at the final assembly process.”
Molding is truly the foundation of the quest. Demanded in this area is the expertise that earned Hideto Yamazaki the “Contemporary Master Craftsman” distinction – for example, striving to raise the precision of finished molds by several microns. The work, however, is hardly limited to this. It begins with adjusting the balance of press machines used to form the molds, zeroing in on issues that emerge at the trial operation stage, inspections of molds equipped with manufactured parts, and numerous other stages. About one full year is reportedly required through completion.
Whatever the case, micron-unit manual adjustment poses a daunting task.
Yet, Mr. Yamazaki appears to be in high spirits as he chuckles: “In my case, I really don’t give it a second thought. Just forge ahead, and it somehow gets done. Rather than that, I truly get fired up when considering how to create a mold with new specifications.”
The pride of simply pushing ahead to bring the precision of molds being worked on to fruition.
“With molds demanding manufacture of particularly small parts, the absence of high accuracy and precision will doom wristwatch operation. Success on this front also leads to confidence and pride. Add to this the sense of joy and accomplishment at seeing the parts created from such molds assembled and adjusted by our colleagues emerging as finished watches.”
Mr. Yamazaki adds that he always feels a sense of deep warmth when seeing people wearing watches that he has been involved with. His gentle expression at this time overlaps with the relaxing landscape of Mt. Iwate. The sense of warmth in Grand Seiko watch hands engaged in the constant and accurate expression of time can likely be traced to the sentiment of those devoted to craftsmanship as they bask in the grand natural setting of Iwate.
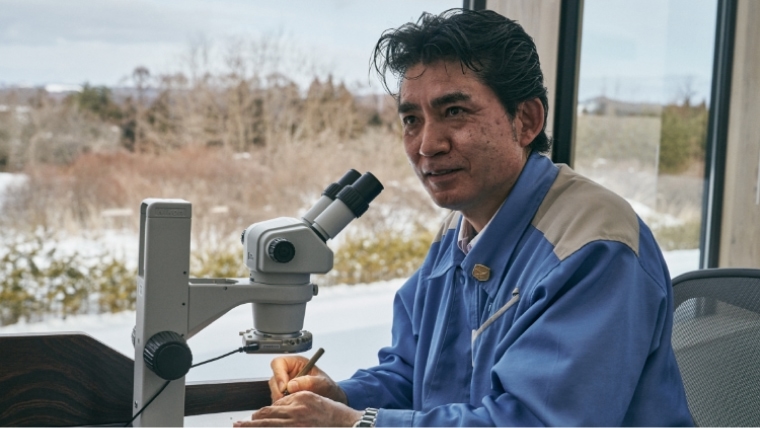

To achieve exterior aesthetics suitable for Grand Seiko movements, the press is subjected to micron-unit adjustment for uniform placement of the five remaining hollowed-out spokes of this wheel.
Shepherding Japanese Mechanical Watchmaking from Iwate into the Future
In 2006, in addition to the in-house meister system, the technical evaluations implemented independently by the company were recognized by the Iwate Prefectural Governor. This marked the launch of the Iwate Watch Meister Evaluation (referring to the work of mechanical watch repair). This has expanded the watchmaking skills and technology steadily passed on in the Iwate region beyond one’s own company, in a move geared to contribute to sustaining these traditions in support of the cultivation of accomplished watch meisters.
Explains President Hayashi: “Morioka Seiko Instruments was certified as the first business in this category, as we were in full accord with the commitment to support the evaluation of specialized skills possessed by companies within the prefecture, including traditional crafts. Rooted in the aim of supporting the quest to pass on this know-how to domestic watchmakers engaged in the crafting of mechanical watches, this authorization is not limited to our own company or group but is rather gaining acceptance on a nationwide scale. This is because, when it comes to this system, we are particular not only about practical skills but also insistent on the need for theory comprising the foundation of the technology.”
There is no doubt that the craftsmanship cultivated and passed down in Iwate is destined to continue to contribute handsomely to the future of the mechanical watch industry in Japan.
New sources of renewable energy,
supplying all power used in watchmaking
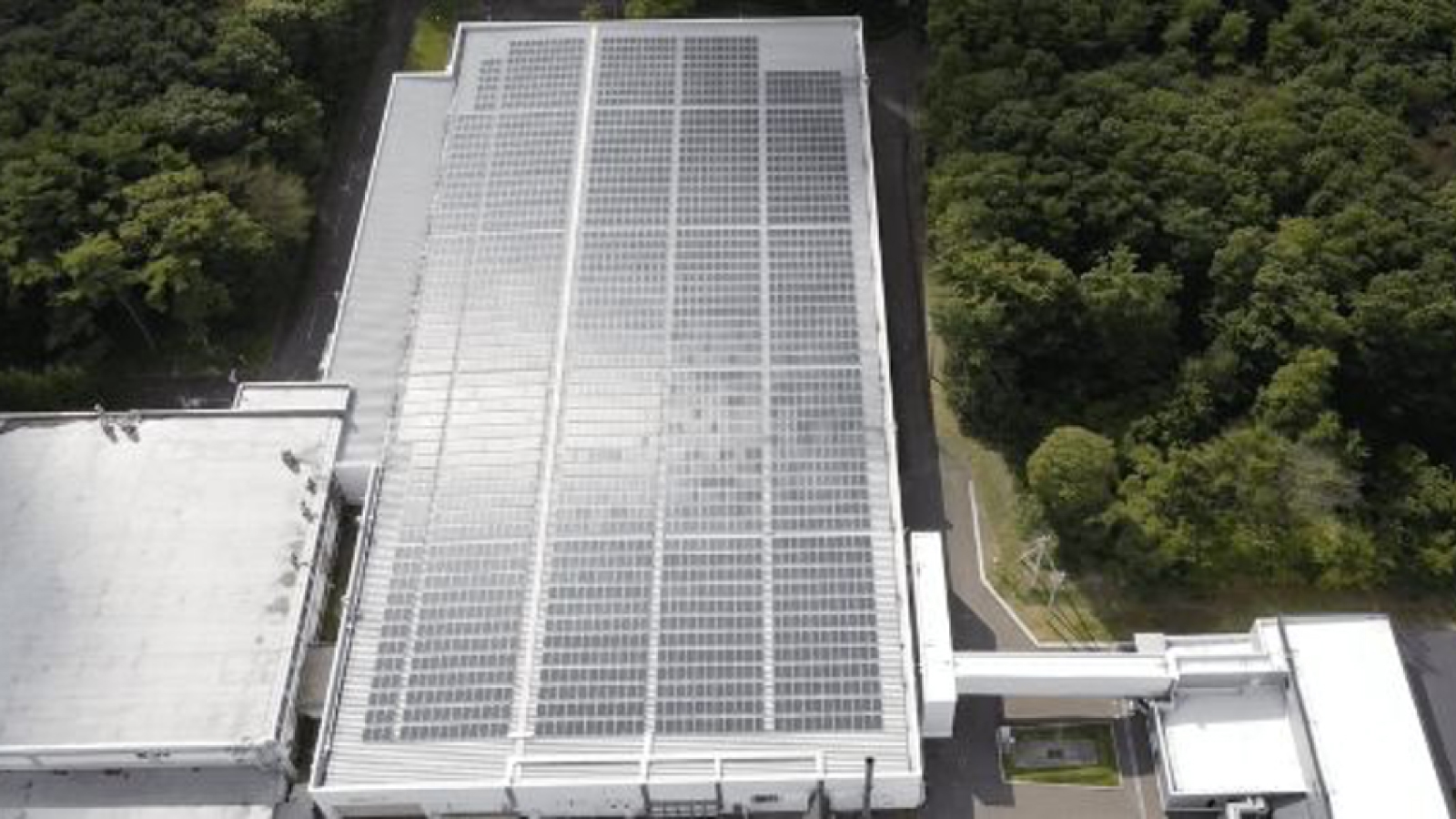
“The Nature of Time” is the Grand Seiko brand philosophy, drawing inspiration from the natural world and the changing seasons in the quest for watchmaking rooted in the true essence of time. To achieve even greater sustainability and coexistence with nature, efforts were made to move to greater renewable energy from December 2020 with the installation of solar panels. In 2021, a successful shift was made to renewable electric power equal to or above the volume of electricity used at Grand Seiko Studio Shizukuishi. Then, from April 2022, with the move to renewable energy for the remainder of the electric power, the shift to green electricity was achieved for 100% of the power used at Morioka Seiko Instruments. In the ongoing quest for harmony with the exquisite natural setting of Shizukuishi Town, greater efforts will be made to achieve sustainable and environmentally friendly craftsmanship.
- Text: Mitsuru Shibata
- Photo: Tetsuya Niikura