Learn more about Calibre 9S
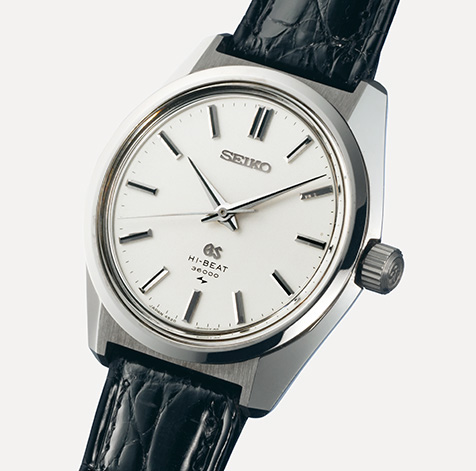
8 beats or 10? A simple question with complex consequences
The faint ticking sound of a mechanical watch is the sound of the jeweled pallet fork engaging with the teeth of the escape wheel in the escapement each time the balance wheel swings. In most mechanical watches, this sound is heard eight times per second, revealing that the movement is an 8-beat. Both the movement of the wearer’s wrist and gravity itself can have a substantial effect on the precision with which the escapement operates so the challenge is to find ways to minimize this effect. The obvious approach would be to increase the number of beats and many watchmakers have taken this route. The fact, however, that there are so few movements in the world that are 10-beat or more is telling, as it demonstrates the extreme difficulty encountered in achieving the required level of durability in the components, given the extra stress on them that the higher number of beats per second imposes. Since the 1960s, Grand Seiko was one of the very few watchmakers to have met this challenge, in the form of the 10-beat 4529 and 6145 movements.
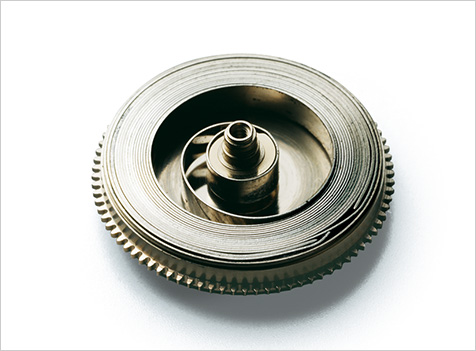
New alloys for higher performance
Increasing the number of oscillations of the balance wheel leads to a proportionately greater consumption of the mainspring’s energy. Shifting from an 8-beat movement to a 10-beat would require 1.5 times more torque and result in a nearly 40 percent loss of power reserve. Increasing impact resistance and efficiently retaining the energy of the balance spring, which is a part of the balance wheel, is also essential. Seiko Instruments had been working with universities and research institutes for over half a century to develop springs. The mainspring of 9S85 is made of Spron 530, an alloy created after some six years of research and development. About five years of hard work was also necessary for the birth of Spron 610 used in the balance spring. The creation of the 10-beat Calibre 9S85 would not have been possible without these two new alloys and springs.
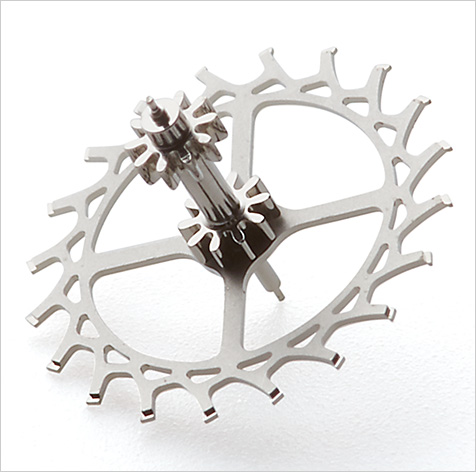
A new manufacturing technique for the most critical components
Enhancing the precision of each part was also crucial for the new 10-beat movement and nowhere is this more true than in the escapement and, in particular, where precision manufacturing could deliver significant gains in performance. The balance wheel in Calibre 9S85 is machined to tolerances of one-millionth of a gram to ensure its precise back and forth rotation. Indeed, the whole escapement of Calibre 9S85 would not have been possible without the use of MEMS (Micro Electro Mechanical System), the ultra-precision machining technology that the company had mastered through its semiconductor manufacturing. This technique allows far greater precision in complex components than can be achieved by cutting. Greater durability was achieved by creating lightening holes in the escape wheel and pallet fork, and also tiered tips on the escape wheel teeth, which successfully improved oil retention performance. Calibre 9S85 may use a traditional escapement but it is an escapement made with the very best of 21st century technology.